锅炉化学清洗规则(二)
来源:未知2012-03-27
4.3清洗前应完成的准备工作:
4.3.1机组热力系统已安装或检修完毕,并经水压试验合格。
4.3.2临时系统安装完毕后,应通过1。5倍清洗工作压力的热水水压试验。清洗泵和各种计量泵及其它转动机械经试运转无异常。
4.3.3储、供水的质量和数量已能满足化学清洗和冲洗的用水需要。清洗用水量可参照附录9《发电锅炉化学清洗用水》。
4.3.4废液处理临时或正规设施应安装完毕,并能有效地处理排放废液。
4.3.5 安装在临时系统中的温度、压力、流过表计及分析仪器应经计量校验合格,并备齐全。腐蚀指示片、监视管等制作完毕。
4.4 清洗系统及其安装
4.4.1 清洗方式应根据清洗介质和炉型来选择,一般盐酸、柠檬酸、EDTA等采用循环清洗,氢氟酸采用开式清洗。
4.4.3 清洗系统的安装应符合下列要求:
4.4.2.1 安装临时系统时,水平敷设的临时管道,朝排水方向的倾斜度不得小于1/200。应保证临时管道的焊接质量。焊接部位应位于易观察之处,焊扫不宜靠近重要设备。
4.4.2.2 所有阀门在安装前,必须研磨,更换法兰填料,并进行水压试验。阀门压力等级必须高于清洗时相应的压力等级。阀门杰身不得带有钢部件。阀门及法兰填料垃采取采耐酸、碱的防腐材料。EDTA清洗时,升温后应检查并紧固循环系统内所有的法兰螺栓。
4.4.2.3 清洗箱的标高及液位应能满足清洗泵的吸人高度,以防泵抽空。安装泵进、出口管道时,应考虑热膨胀补偿措施,不便水泵受到过大的推力。
4.4.2.4 可在锅筒上设临时液位计及液位报警讯号。根据循环流速的要求,在锅筒下降管口设节流装置,并将锅筒放水管加高。
4.4.2.5 清洗系统中的监视管段应选择脏污程度比较严重,并带有焊口的水冷壁管,其长度为350-400mm,两端焊有法兰盘,监视管段一般安装于循环泵出口,必要时高压锅炉还应在水冷壁管处设置监视管装置。
4.4.3 不参加化学清洗的设备、系统应与化学清洗系统可靠地隔离,要求:
(1)拆除锅筒内不宜清洗的装置;
(2)水位计及所有不耐腐蚀的仪表,取样、加药等管道均应与清洗液隔离;
(3)过热器若不参加清洗,应采取充满除盐水等保护措施。
4.4.4 为维持锅炉清洗液的温度,应严密封闭炉膛及尾部烟道出口。
4.4.5 在锅筒不位监视点、加药点及清洗泵等处,应设通讯联络点。
4.4.6 应将清洗系统图挂于清洗现场。系统中的阀门应按图纸编号,并挂编号牌。管道设备应标明清洗液流动方向,并经专人核对无误。
4.4.7 系统安装完毕后应清理系统内的砂石、焊渣和其它杂物。
4.5 电站锅炉化学清洗工艺
一般工艺步骤为:系统水冲洗、碱洗、碱煮转型、碱洗后的水冲洗、酸洗、酸洗后的水冲洗、漂洗私钝化,其清洗工艺的主要控制条件见附录10《电站锅沪化学清洗工艺综合表》。
4.5.1 系统水冲洗
新建锅炉,在化学清洗箭必须进行水冲洗。可用过滤后的 澄清水或工业水进行分段冲洗,冲洗流速一般为0.5-1.5m/s。冲洗终点以出水达到透明无杂物为准。
4.5.2 碱洗或碱煮
4.5.2.1 新建锅炉仅实施碱煮的,在煮炉过程中,需由底部排污2-3次巳煮炉结束后进行大量换水,待排出水和正常锅水的浓度接近,且pH值降至9左右,水温降至70-80oC,即可将水全部排出。煮炉后应对锅炉进行内部检查,要求金属表面无腐蚀产物和浮锈,且形成完整的钝化保护膜。同时应清除堆积于锅简、集箱等处韵污物。
4.5.2.2 酸洗前的去油碱洗,一般应采用循环清洗或循环与浸饱相结合。碱洗后用过滤澄清水、软化水或除盐水冲洗,洗至出水pH值垂8.4,水质透明为止。
4.5.2.3 若水垢申硫酸盐、硅酸盐含量较高,为提高除垢效果,可在酸洗前按3.4.3的方法,先进行碱煮转型。
4.5.3 酸洗及酸洗后的本冲洗
4.5.3.1监视管段渍在清洗系统进酸至预定浓度后,投入循环系统,并控制监视管内流速均被清洗锅炉水冷壁管内流速相近。
4.5.3.2 酸洗时必须按清洗方案严格监控酸洗液的温度、循环流速,锅筒和酸槽的液位等,并每小时记录一次。按时巡回检查,如实记录出现的问题。
4.5.3.3 当每一回路循环清洗到预定时间时,应加强酸液浓度和铁离子浓度的测定。当各回酸洗液中酸液浓度和铁离子浓度趋于稳定和平衡,预计酸洗将绪粟蹲,可取下监视管检查清洗效果。若管段内仍有污垢,应再把监视管段装回系统继续酸洗。至监视管段内清洗于净,应再循环1小时,方可停止酸洗。
4.5.3.4 为防止活化金属表面产生二次锈蚀,酸洗结束时,不得采用将酸直接排空再上水的方法进行冲洗,可用纯度大于97×lO-2,的氮气连续顶出废酸液,也可用除盐水顶排出废酸液。酸液顶出后采用变流量水冲洗,冲洗时水流速应达到清洗流速的一倍以上,尽可能缩短冲洗时间。水冲洗至排出液的PH值为4-4.5,含糊铁量小于50mg/L为止。
4.5.3.5 对沉积物量或垢奴较多的锅炉,酸洗后如有较多未溶解的沉渣堆积在清洗系统及设备的死角时,可在水冲洗 至出水PH值为4-4.5后,再排水用人工方法清除锅炉和酸内酌沉渣。用此法冲洗后,须经漂洗才能进行钝化。
4.5.4漂洗和钝化
4.5.4.1 采用氮气或水顶酸,即在锅内金属未接触空气的情况下可免做漂洗,若退酸水确洗后有二次锈蚀产生的,则须进行漂洗。
4.5.4.2 锅炉酸洗后必须进行钝化(除EDTA清洗钝化一次完成外)。如漂洗后钝化的,漂洗液申的铁离子总量应小于300mg/L若超过该值,应用热的除氧水更换部分漂洗液至铁离子含量小于该值。 钝化过程中,应定时取样化验,如钝化液浓度降至起始浓度的二分之一时,应及时适量补加钝化液。
4.6 清洗后的内部检查和系统的恢复
4.6.1 清洗后,应打开锅简、集箱和直流炉的启动分离器等能打开的检查孔,彻底清除洗下的沉渣。
4.6.2 一般应对水冷壁进行割管检查,判断清洗效果。对于运行锅炉应在热负荷较高部位割管;对于新建锅炉应在清洗流速最低处,割取带焊口的管样。对于新建锅炉,如能确定清洗效果良好的,也可视具体情况免作剖管检查。
4.6.3 清洗检查完毕后,应将锅筒内和系统中拆下的装置和部件全部复位,并撤掉所有的堵头、隔板、节流装置等,使系统恢复正常。
4.7 循环清洗中的注意事项
4.7.1 酸洗时,应维持酸液液位在正常水位线上,水冲洗时,应维持液位比酸洗时液位略高一些,钝化时的液位应比水冲洗的液位更高。
4.7.2 清洗液的循环方式与锅炉的结构和受热面结垢的程度等因素有关。对结垢严重的回路应先进行循环清洗,其余回路静止浸泡,待该回路循环一定时间后,再依次倒换。必要时可对结垢严真的回路重复进行循环清洗。
4.7.3 为了提高清洗效果,每一回路最好能正反向各循环一次(取决于炉管和锅筒连接的情况)。如通向锅筒的某些导汽管位置较高,只能进行单向循环时,酸液应由高位管进人,低位管排出。
4.8 清洗后的保养
锅炉清洗后如在一个月内不能投大运行,应采取下列之一的防腐蚀方法进行保护;
4.8.1 液相保护法:
氨液保护:钝化液排尽后,用l×lO-2的氨液冲洗至排出液不含钝化剂,再用(0.3-0.5)×lO-2的氨液充满锅炉,进行保护。 氨一联氨溶液保护:将浓度为500mg/L的NH3,300-500mg/L的N2H4,PH值为9.5-10的保护液充满锅炉,进行保护。
氨一乙醛肪(C2H5ON)溶液保护:将浓度为300-500mg/L的C2H5ON,加氨水调pH值,PH值为9.5-10的保护液充满锅炉,进行保护。
4.8.2 气相保护法:
在严冬季节,可采用充氮法保护或气相缓蚀剂保护。使用的氮气纯度应大于于99.9×10-2,锅炉充氮压力应维持在0.02-0.05MPa。
4.9 清洗过程的化学监测及留样分析项目
4.9.1 清洗系统中应在有代表性的部位设置便于操作的监视取样点。一般锅筒式锅炉的监视取样点布置在系统回路的入、出口处;直流锅炉应在下列各部位分别布置取样点:(1)凝结水处理系统出口;(2)低压加热器出口;(3)除氧器水箱出口;(4)高压加热器出口;(5)水冷壁管出口;(6)启动分离器出口;(7)高温过热器出口;(8)再热器出口。
4.9.2 清洗过程应定时对清洗液进行取样化验,化验方法见附录7《清洗过程化学监测分析方法及其监测的项目一般规定如下:
4.9.2.1 煮炉和碱洗过程:锅筒式锅炉取盐段和净段的水样,直流炉取锅炉出、入口水样,每2小时测定碱度和PO43一次;换水时每2小时测定碱度一次,直至水样碱度与正常锅水碱度相近为止。
4.9.2.2 碱洗后的水冲洗;每15分钟测定一次出口水的PH值,每隔30分钟收集一次冲洗出口水留样分析。
4.9.2.3 循环配酸过程:每10-20分钟分别测定酸洗回路出、入口酸浓度一次,直到浓度均匀,并达到指标要求为止。
4.9.2.4 酸洗过程:每30分钟分别测定酸洗箱出口、酸洗回路出、入口的酸浓度和Fe3+及Fe2+的含量。
用EDTA清洗时,每1小时(酸洗后期每30分钟)分别测定酸洗回路出口、入口清洗液中EDTA的浓度、pH值和总铁含量。
开式酸洗系统在开始进酸时,每5分钟测定一次锅炉出、入口酸液的浓度。酸洗过程中,每10分钟测定一次锅炉出、入口酸液的酸浓度及含铁量。
为了计算洗出的铁渣量,在酸洗过程中还应定期取排出液混合样品,测定其悬浮物和总铁量的平均值。
4.9.2.5 酸洗后的水冲洗:每15分钟测定一次出口水的PH值、酸浓度。冲洗接近终点时,每15分钟测定一次含铁量。
4.9.2.6 漂洗过程:每30分钟测定一次出口漂洗液的酸浓度、PH值和含铁量,并在漂洗结束时留样分析。
4.9.2.7 钝化过程:每1-2小时测定一次钝化液浓度和PH值。
4.9.2.8 过热器水冲洗过程:分别从饱和蒸汽和过热蒸汽取样,每30分钟测定一次碱度,PH值和电导率。
4.9.2.9 留样分析项目:碱洗留样,主要测定碱度、硅酸化物和沉积物含量;酸洗留样,主要测定悬浮总铁量;漂洗留样,主要测定沉积物含量。
4.10 清洗质员验收要求
4.10.1 被清洗的金属表面应清洁,基本上无残留氧化物和焊渣,无明显金属粗晶析出的过洗现象,不允许有镀铜现象。
4.10.2 用腐蚀指示片测量的金属腐蚀速度的平均值应小于6g/(m2·h),且腐蚀总量不大于60g/m2。
4.10.3 锅炉清洗表面应形成良好的钝化保护膜,金属表现不出现二次浮锈,无点蚀。
第五章 清洗废液的处理
5.1 锅炉清洗废液应经处理后才能排放。废液处理和测定方法见附录11《清洗废液的处理和F-含量的测定方法》和附录10《电站锅炉化学清洗工艺综合表》。严禁排放未经处理的酸、碱液及其它有毒废液,也不得采用渗坑、渗井和漫流的方式排放废液。
5.2 锅炉化学清洗废液的排放应依据当地受纳水域功能的要求,按GB8978-1996《污水综合排放标准)的规定控制污染物排放浓度。其中主要的有关指标和最商允许排放浓度如下:
受纳水域
污水排放执行标准
PH
悬浮物SSmg/L
化学需氧量CODmg/L
氧化物(mg/L)
磷酸盐(mg/L)
Ⅲ类水域或二类海域
一级
6-9
70
100
10
0.5
Ⅳ、Ⅴ类水域或三类海域
二级
6-9
150
150
10
1.0
二级污水处理城镇排水系统
三级
6-9
400
500
20
注:1.Ⅲ、Ⅳ、Ⅴ类水扯按GB3838-88《地面水环境质量标准》划分;
2.二、三类海域按GB3097-82《海水水质标准》划分;
3.排入未设置二级污水处理厂的城镇排水系统的污水,应根据受纳水域的功能要求,分别执行一级或二级标准。
第六章 安全基本要求
6.1 清洗单位须根据本单位具体情况制定切实可行的安全操作规程。锅炉清洗前,工作人员必须学习并熟悉清洗的安全操作规程,了解所使用的各种药剂的特性及急救方法,并做好自身的防护。
6.2 清洗现场应备有可靠的消防设备、安全灯、充足的照明、急救药品和劳保用品。
6.3 清洗时,禁止在清洗系统上进行其它工作,酸洗时不准进行明火作业。在加药场地及锅炉顶部严禁吸烟。清洗过程中,应有专人值班,定时巡回检查,随时检修清洗设备的缺陷。
第七章 附 则
7.1本规则由国家质量技术监督局负责解释。
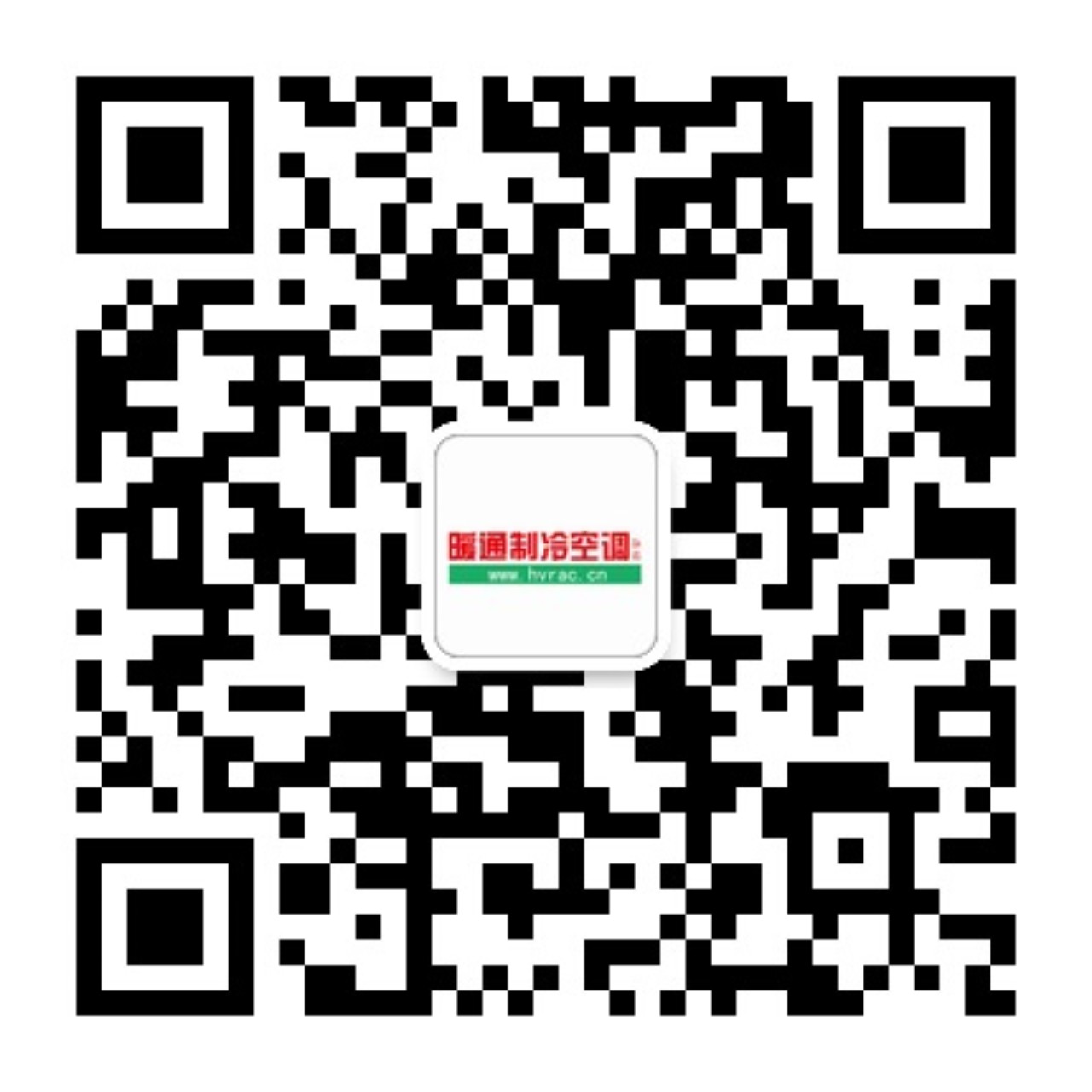
扫码关注暖通制冷空调杂志官方微信公众平台
(微信号:hvrac200561)关注最新行业资讯!